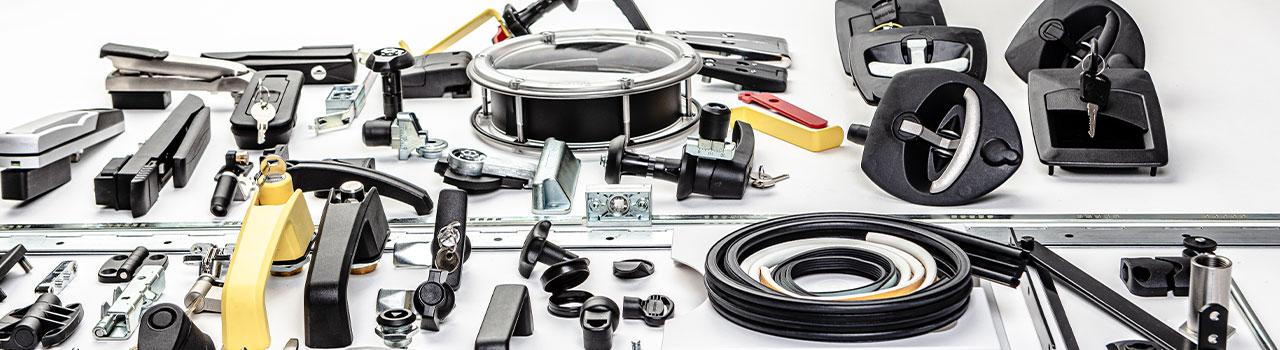
Material & Processes
MAKING IT THE RIGHT WAY
Designing and manufacturing our solutions involves many different materials, produced and treated in a vast number of ways. Below, we have gathered some of the more common materials and processes, as a glossary.
Should you have any questions - please do not hesitate to contact us.
Acid proof steel
Acid proof or acid resistant steel contains iron and chromium, and additionally some nickel and/or manganese as well as smaller quantities of other metals such as molybdenum, niobium and titanium.
Acid proof steel is used in environments with more challenging chemical exposures, such as a maritime environment and when items come in contact with acids.
The steel alloy containing both chromium and nickel is also known as nickel-chromium steel.
If nothing else is stated, the classification Acid proof steel refers to the European Standard EN 1.4404, which corresponds to American Iron and Steel Institute standard AISI 316L.
Aluminium
Aluminium is frequently considered a non-corrosive metal, but this is not entirely accurate. Aluminium corrodes but between pH 4 and pH 9 it forms a passive oxide film that protects the material. Outside of this pH norm aluminium corrodes quickly.
Alloys corrode quicker than pure aluminium, and the fastest corrosion occurs when it contains copper. However, aluminium can handle sulphuric acid, nitrates and acetic acid thanks to the formation of either a passive oxide film or acetates that isolate the aluminium from the oxidizing substance.
Upon contact with other metals corrosion can occur if the environment is damp. This is true in for instance contact with copper or iron.
Contact with stainless steel is on the other hand harmless under normal conditions.
The Industrilas product inventory offers hinges and rod latches made of aluminium.
Anodizing
Anodizing turns the surface layer of a metal into an insoluble oxide which provides corrosion protection, decorative surfaces, good adherence for enamels and other surface treatments, as well as certain electrical and mechanical characteristics.
Aluminium is the most common metal for anodizing, but magnesium, zinc, and titanium are also used for this purpose. The electrolyte solution consists of diluted sulphuric acid or chromium acid.
Biomaster
Antimicrobial is a substance that will reduce or destroy the presence of microbes such as bacteria and mould. The protection provided by the substance Biomaster guarantees fast and effective antimicrobial protection for the active lifespan of the product, keeping highly touched surfaces clean and reducing bacteria count and the risk of cross-contamination. Biomaster is added to powder coating and can easily be incorporated into any plastic, textile, paper, paint or coating.
Bonderite NT
This a modern method of pre-treatment for powder coated items.
The method is based on nanotechnology and is a multi metal process adapted primarily for zinc, aluminium and steel.
The process offers improved corrosion protection compared with for instance iron phosphating, as well as excellent adhesion for application of powder.
The four rinse stages assure a better process stability. Reverse osmosis is employed to de-ionize the water, which involves a membrane technique that requires a minimal use of chemicals.
Brass
Brass is a copper alloyed with zinc. Other alloy elements may also be present. However, the most common brass consists of 65% copper and 35% zinc.
Industrilas primarily uses brass for housing nuts, cylinders, keys, plates and hinge items.
Chroming
Chroming is usually done on Industrilas' metal products to provide a hard surface and corrosion protection.
The method may also be used for decorative purposes as different colours can be obtained depending on the chromate concentration in the bath:
- metallic shiny
- light blue
- yellow
- green
- bronze
- black.
The baths contain among other things chromic acid, chromates, cyanides and acids.
Construction Steel
The distinguishing characteristics of the general construction steels are their toughness and good response to welding. These materials have been given improved cuttability through cold work and/or lead additives.
Industrilas uses S235JR (SS 1312) in for instance cams, if nothing else is stated.
S235JR (SS 1312) characterizes cold drawn flat and round bars with good surface finish that are easy to work and weld on.
Construction steels are mostly used in items with moderate strength requirements.
Copper
Copper is 100% recyclable without losing any of its properties. According to newly acquired data 34% of the 22 million tons of copper used globally every year come from recycled material.
The lifespan of different copper products vary greatly, from 100 years or more in buildings, to just a few years in electronic equipment. In damp air, especially with air pollution present, a brown oxidation film builds up, which later transforms to a green patina. This thin layer protects against further corrosion.
Common copper alloys are brass, bronze and silver plate.
Industrilas mainly uses copper in custom ordered items.
Deburring
Deburring is performed to remove burrs, smoothen edges, eliminate forge scales or improve the surface quality of objects.
The items are placed in a rotating drum or a vibrating container and is either circulated through the machine “plain” or with the addition of a grinding agent.
The deburring process can be performed wet (most common) or dry. During wet tumbling water or oil is used with added chemicals and grinding agents, which can consist of aluminium oxide, silicon carbide, steel, etc.
Degreasing
The surface treatment is often the last stage in the manufacturing process, which generally has been preceded by some form of mechanical work where oil has been used for lubrication or cooling. Oil may also be used as corrosion protection during interim storage of the items.
Alkaline and acidic parts cleaning, or degreasing with a solvent (trichloroethylene) is performed to remove oils, grease etc., from the item’s surface before the final stage of surface treatment (see list above).
For the same reason steeping is employed to remove forge scale, rolling skin, rust and other types of oxidation layers. Steeping is commonly accomplished by submerging the item in one or more acids, but also complex-forming alkaline salts and steeping pastes may be used. (Even electrolyte steeping may occur.)
Delrin
Delrin is a particular manufacturer’s trade name for Polyoxymethylene (POM).
This is a plastic that is often used as a substitute for metal items. The primary characteristics are low weight, low friction, durability and it can be used in temperatures up to 90˚ centigrade.
Certain hinge pins in the Industrilas product inventory are made of Delrin/POM.
ED Coating
ED coating (electrolytic dip coating) is an alternative to powder coating. This coating is employed when the required tolerances are very precise.
ED coating is an acrylic/urethane polymer applied cathodically through electrophoresis. The surface becomes decorative with a relatively high shine. ED coating can be applied to steel, aluminium, die cast zinc, hot-galvanized steel, electrolytically zinc plated steel surfaces, etc.
The method makes it possible to cover the metal with an evenly regulated and extremely thin surface layer (approximately 20-22 μm) with excellent adherence to the entire surface. The UV-resistant coating layer is void of pores and provides excellent corrosion protection as well as great wear resistance.
ED coating has been classified by the Swedish Occupational Health and Safety Board as one of the most environmentally conscious coating procedures available.
Industrilas includes ED coating as an alternative surface treatment for a number of items in the product inventory.
EPDM
EPDM rubber (Ethylene Propylene Diene M-class rubber) is an elastomer characterized by its wide range of applications.
EPDM rubber is used at Industrilas for different types of strips, sealants and gaskets. It exhibits good resistance to water and alkalis, but not oil, gasoline and concentrated acids.
Fixed Gasket (FIPFG)
As part of the product development at Industrilas an increasing number of products contain an injected, fixed porous gasket called FIPFG (Formed In Place Foam Gasket), also known as a ”PUR”-gasket (polyurethane gasket).
The method involves robotic application on the item of a bead of liquid gasket material, consisting of a two-component polyurethane. As the gasket cures it also expands, turning into an attached, flexible, porous gasket, which offers a reliable barrier against influence from external elements.
The fixed gasket simplifies assembly, reduces the number of loose items and offers improved sealing. The polyurethane is also available in special versions to achieve approval to a particular UL-norm or to the VDI 6022-standard.
Flat Gasket
A flat gasket is used to seal between for instance the lock and the door of a monitor housing in order to obtain IP65 in Industrilas' products.
The flat gasket is made of a blend of NBR (Nitrile Rubber) and SBR (Styrene-Butadiene Rubber). It has good resistance to chemical and oil.
The gasket can also be exchanged for other materials to achieve approval to a particular UL-norm or to the VDI 6022-standard.
Free cutting steels
The main requirement of these steels is good cuttability. The cutting speed needs to be kept optimally high. The shape of the filings needs to be short to make them easy to transport away from the point of cutting.
Industrilas uses 11SMnPb30 (SS 1914) in for instance rod latches in the standard inventory. 11SMnPb30 (SS 1914) characterizes a lead-alloy freecutting steel of moderate strength. Its cuttability is excellent, and it produces short filings. It needs to be worked at a high cutting speed for best results.
GF 30
Glassfiber reinforced polyamid (with 30 % added glassfiber). See also Polyamide Plastics (PA).
Hygiene Applications
This refers to the standards “EN ISO 14159 - Safety of machinery” and “Hygiene requirements for the design of machinery (ISO 14159: 2002)”; German version; “EN ISO 14159: 2008”.
A “hygienic design” is the cleaning friendly or easy clean design of parts, components and production equipment. In the structural design requirements are taken into account to the ease of cleaning, so that areas can be avoided in which dirt can accumulate and can pose a risk to the product (eg food).
Furthermore, the product design should facilitate an effective and simple cleaning of the parts, and are often made of materials that can stand up to disinfectants and to other ways of disinfecting machinery, for instance steam. Hygienic Design is an important element for ensuring the food quality.
Industrilas provides latches for machine casings or enclosures that meet the requirements of the hygiene standard above.
An example product is our Quarter-Turn Hygiene latch in Stainless Steel. Click the button to have a look.
Industrilas IP-classifications
IP54 = Dust protected and splash-proof - this is considered the standard issue.
IP65 = Dust tight and water jet-proof - the higher classification of intrusion protection is obtained by sealing for instance a lock’s housing with an O-ring and a flat gasket or a fixed gasket.
It should also be mentioned that Industrilas has a few other special classifications. Most notable are products used in high-hygiene applications, for instance when our products are used in the food manufacturing industry:
IP69K = Dust tight and protected against close-range high pressure, high temperature water jets.
IP Sealing Classifications
The Industrilas inventory features two main intrusion protection classifications.
If a product is rated to seal at IP65 it has either been tested by an independent laboratory, or the product is so similar in construction to another tested product that it could safely be classified as IP65. However, it should be noted that it is the complete product that is rated for intrusion protection, including the cabinet or product that the item is built into.
Industrilas can only guarantee that its products live up to their stated IP standards if those products are built in and used in a correct manner.
The IP classification is designated by two numerals, with the following significance:
- The first number indicates the degree of protection against touch and intrusive objects.
- The second number indicates the degree of protection against intrusive water.
The higher the number, the better the protection.
NEMA Sealing Classifications
In North America intrusion protection is classified according to the standards of NEMA (National Electrical Manufacturers Association). If an Industrilas product is rated to seal at NEMA 4 it has either been tested by an independent laboratory, or the product is so similar in construction to another tested product that it could safely be classified as NEMA.
IP65 roughly corresponds to NEMA 4, but the ratings are not directly equivalent between the two standards.
Nickel Plating
This process is primarily used on decorative surfaces and for corrosion protection, but also as a substrate for chrome, gold and silver plating. The baths usually consist of sulphates, chlorides and boric acid (= Watt’s solution).
O-ring
O-rings are often used to seal between handle and insert or housing in order to obtain sealing classification IP65 in Industrilas' products.
The O-rings used by Industrilas are often made of NBR (Nitrile Rubber), a material with good chemical resistance and very good oil durability. We can also supply products with O-rings made from other materials than NBR if you need a product to achieve UL-approval etc.
Passivation
This is a process whereby a protective layer is obtained on metals, especially stainless steel and copper, through submersion in an acidic solution.
PHOSPHATING, an alkaline process that is performed to provide corrosion protection, a foundation for the lacquer coat, corrosion protection underneath a layer and/or to obtain lubrication. It is primarily iron and zinc that are given a phosphate coating.
The most common methods of phosphate coating are, according to the content of the baths, iron, zinc and manganese, and they usually take place through spraying or submersion.
Plastic Injection Moulding
Injection moulding is a manufacturing process for items in various thermo-plastics, or plastics that become liquid at high temperatures. The machine consists of an injection unit and a mould-closing unit, and a mould unique to each product or tool. The injection unit is fed with ground-up plastic through a funnel that leads to a heated cylinder. The melting point is usually between 175˚ and 300˚ centigrades.
The molten plastic is pushed forward with a screw that also functions as a piston. The molten plastic is portioned out and injected in the mould in an intermittent process. The mould is kept closed until enough plastic is filled into it and until correct pressure has built up (50- 150 MPa). Now, the plastic is cooled off, the mould is split open and the part is removed, whereafter the process is repeated.
Important factors are the temperature of the molten plastic, the pressure in the injection unit, the temperature of the mould, the cooling-off period, and the dimensions and design of the mould itself.
Polyamide Plastics (PA)
Industrilas' products are also manufactured through injection moulded Polyamide 6.
The auto industry and makers of household appliances and office equipment are main users of PA due to its characteristics:
- wear-and -tear endurance
- toughness
- resistance to inorganic compounds, oils, greases, gasoline and organic solvents
- can be sterilized with steam
- and has a low friction coefficient.
The standard Industrilas Polyamide 6 (PA6) is modified for toughness with various amounts of glass fibre reinforcements, usually 30% (GF30), to additionally optimize the characteristics of the product.
Industrilas has chosen PA6 particularly for its high impact toughness and good mechanical characteristics. The temperature range for use of items made of PA6 is -30˚ to +70˚ centigrade.
Industrilas also injection moulds items from other plastics, such as PC, POM, ABS, PP, PE and PS. Housings, inserts, handles, keys and hinges are all examples of products manufactured out of PA, even though all these items are available in other materials as well.
Powder Coating
Industrilas aspires to control as many production processes as possible, and consequently in-house powder coating capability has also been obtained.
The choice of method is based on several criteria, prioritizing product quality and environmental concerns. The preparation method is Bonderite, and the powder application is performed in a chamber with modern application equipment that charges the powder electrostatically.
The applied powder is especially formulated for coating of porous items, such as die cast or zinc plated steel, where the risk of blister build-up and pinholes are prevalent during the tempering process.
The Industrilas standard powder contains polyester as a bonding agent, which renders the finished products extra resistant to bleaching by sunlight. After the coating the powder is cured for 20 minutes in an electrically heated furnace. The advantages of an electric furnace are primarily better process stability, and a less sensitive coating process of for instance light-coloured items.
PVC
Polyvinyl chloride (PVC) is one of the most common kind of plastic. It is a thermoplastic polymer made of several connected vinyl chloride molecules, and constitutes one of the basic plastics. However, a material that only contains polyvinyl chloride is rather stiff, so a softening agent is added to the polymer.
The Industrilas inventory offers edge protection in PVC and so-called carriers of certain sealing profiles.
Silicone
This is the collective name for basically inorganic polymers based on strands of silicon and oxygen. Silicon does not conduct electricity, does not dissolve in water and is relatively resistant to the effects of chemicals.
The Industrilas inventory offers sealing profiles from silicone. These are separately stored and delivery will be after consultation with the customer.
Sintering Metals
Sintering is the process of compacting and forming a solid mass of material by heat and/or pressure without melting it to the point of liquefaction. The metal powder is pressed into a mold in the shape of the detail.
The pressing produces a so-called "green body" containing a great amount of pores. In the sintering process the green body is heated so many of the pores are closed and the item takes on its ultimate mechanical characteristics.
Sintering produces smooth surfaces, and items with complex shapes can be manufactured without the need for much additional work. This can be done with different materials such as stainless steel, and so on.
Industrilas uses sintered items as for instance cogwheels and pinions.
Solid Components
Since 2008 Industrilas has used SolidComponents™. This allows customers an internet solution with a digital product catalog with CAD support and instant access to 3D CAD models of all the products of our standard program.
The system supports all major CAD systems. To download CAD data, just click on the part number and choose your CAD platform, and the file is generated immediately. Via a product configurator you can also create your own CAD models.
SolidComponents™ is currently used by design engineers in over 140 countries, which together generate millions of different CAD models every year.
These are the supported formats in 3D and 2D:
- SolidWorks Pro/E
- Sat
- Step
- Parasolid
- Iges
- Dxf
- Dwg
- SOLIDWORKS
At Industrilas, we use SolidWorks 3D CAD system. On this foundation, we have developed solutions for demanding latch-, hinge- and gasket applications for more than 20 years. Our design department works with the latest developing and simulation tools, for instance when designing multi-axis hinges.
All our combined resources are available to you as we help you develop products that best meet your needs.
Stainless Steel
Certain demanding environments require a more durable material.
The corrosion resistance of stainless steel comes from the steel being alloyed with chromium. When the chromium content exceeds approximately 10.5% a thin film is formed on the steel that passively protects the underlying steel from further oxidation, or rusting. In case of damage to the surface of the steel the top film of protective chromium oxide forms again very quickly.
Industrilas has a large assortment of stainless versions of locks, handles and hinges. If nothing else is stated, the classification ”Stainless Steel” refers to the European Standard EN 1.4301, which corresponds to American Iron and Steel Institute standard AISI 304.
V-0
The polyamide used by Industrilas (PA6) is reinforced with glass fiber for increased toughness. The amount of glass fibers varies, but is usually 30% (GF30).
The polyamide may also be modified to fulfil the standard V-0 in accordance with UL 94 (flammability: self-extinguishing of the flame within 10 seconds). Industrilas use the PA6 particularly due to its high impact resistance and good mechanical properties.
See also “Polyamide Plastics (PA)”.
VDI 6022 Part 1 (2006-04)
The guideline series VDI 6022 applies to all air-conditioning systems, the rooms or common areas in rooms intended to be occupied by people more than 30 days per year or regularly for more than two hours per day.
It applies to all equipment and appliances and their centralized and decentralized components (also HVAC-units such as cooling towers, which will affect the supply air). The Directive applies also in situations for air exhaust ventilation equipment when this may influence the supply air when using heat exchangers or similar.
Industrilas supplies products such as inspection windows for ventilation systems (HVAC-units) made of materials with the proof of the required microbial inertness according to VDI 6022. See index code 5-255.
Zinc (Zamak 5, Z 410)
Industrilas' product inventory includes die cast items made of zinc.
The alloy that is utilized is a mixture of zinc, aluminium, magnesium and copper. Industrilas uses the alloy ”Zamak 5” due to its superior qualities in the combination ease of casting/surface finish.
Housings, inserts, handles, keys and hinges are all good examples of suitable die cast products, even though all of these are also available in other materials.
In certain demanding environments zinc is not the recommended metal, such as in a marine environment, or external vehicle components and situations where there is a risk of severe mechanical wear.
Zinc die casting
Die casting is a manufacturing process that involves forcing hot, molten metal into the mould cavity made from a tool, which in turn can have varying degrees of design detail.
When the metal, under pressure, has solidified, it is ejected from the mould cavity and the item is finished. After vibratory deburring and drying it is ready for surface treatments.
The primary advantages of die casting are the ability to stay within precise dimensional requirements, cast intricate items with good strength and corrosion resistance and obtain a fine surface finish.
Zinc Plating
This process is the most common metal plating method, offering corrosion protection for steel items.